There are many kinds of casting defects, and the analysis of casting defects is an important part of casting production process control. After the casting defects are found through inspection, it is necessary to start with the analysis of the characteristics of the casting defects and accurately locate the defect types with the help of a variety of detection methods, which is the focus and difficulty of the analysis. On this basis, according to the on-site production process conditions of the workshop, find out the specific causes of defects, and put forward improvement plans and measures.
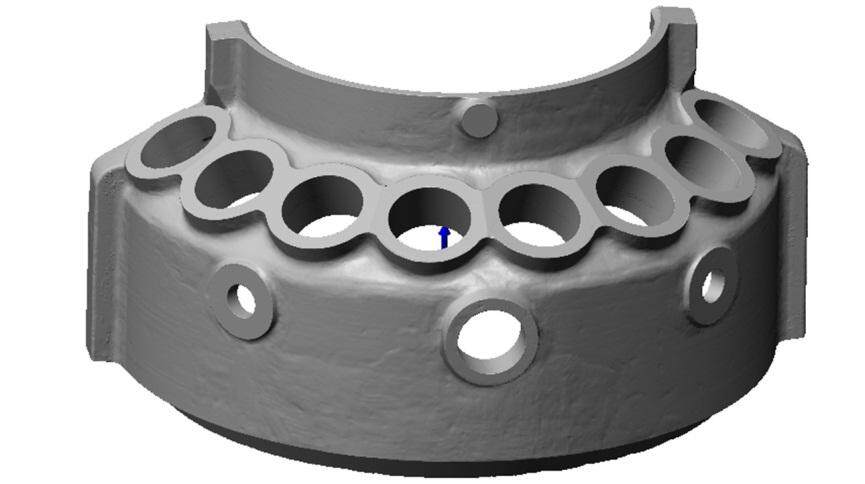
Pores and pinholes
- Pores can be divided into invasion pores, precipitation pores and reaction pores according to the generation mechanism. When the pouring temperature of the gas dissolved in the molten metal is low, it is too late for the gas to escape upward; The furnace charge is wet, rusty, greasy, and contains inclusions that are easy to produce gas; The iron flume and ladle are not dried; The moisture content in molding sand exceeds the standard and the permeability is poor; The paint contains too much gas generating material; The core is not dried or cured, and the storage time is too long, moisture absorption and moisture return, and poor ventilation; During pouring, there is flow cut-off and gas entrapment.
- Prevention methods. The furnace charge shall be dried, trusted, and degreased; The coke has moderate lumpiness, high fixed carbon content, low sulfur content, and less ash, to improve the temperature of the discharged liquid; Inoculants, spheroidizing agents, and tools used should be dried; Prevent excessive oxidation in the smelting process. When smelting ductile iron, try to reduce the sulfur content in the raw molten iron; The mixing of molding sand should be uniform, and the water content in molding sand should be strictly controlled; On the premise of ensuring the strength, try to reduce the amount of clay to improve the permeability of molding sand; Minimize the content of gas generating substances in molding sand; In the process of drying molds and cores, the drying degree should be controlled; When making molding sand, the sand shall be pounded evenly, and the exhaust of mold and core shall be unobstructed; The design of gating system should be reasonable, and the height of sprue should be increased to improve the static pressure of liquid metal; The gas outlet riser should be placed at the highest part of the cavity and where the gas in the cavity is not easy to be discharged.
Shrinkage and porosity
- The liquid and solidification shrinkage of the alloy is larger than the solid shrinkage, and it cannot be supplemented by enough liquid metal during the liquid and solidification shrinkage; When the pouring temperature is too high, it is easy to produce concentrated shrinkage cavities, and when the pouring temperature is too low, it is easy to produce dispersed shrinkage porosity; The connection between the pouring system and riser and the casting is unreasonable, resulting in large contact hot spots; The rigidity of the mold is low, and the mold wall expands and deforms under the pressure of liquid metal and the expansion force when graphite is precipitated.
- Prevention methods. Correctly design the position of ingate, riser, and chill to ensure that the casting is continuously supplemented with liquid metal during solidification; Improve the structure of the casting, so that the casting is conducive to feeding; Ensure that the mold has sufficient rigidity, and use the dry mold for larger castings to prevent the mold wall from expanding outward.
Cold crack
- The wall thickness of castings varies greatly, and there is no transition between thin and thick walls, which changes suddenly, resulting in large differences in cooling speed, inconsistent shrinkage, and local stress concentration of castings; High phosphorus content in the molten metal increases brittleness; The residual stress inside the casting is large, and it cracks when subjected to mechanical force.
- Prevention methods. Strive to make the wall thickness of the casting uniform, so that the cooling rate of each part of the casting tends to be the same as far as possible; Try not to obstruct the shrinkage of castings; Improve the melting quality of the alloy and reduce harmful elements and non-metallic inclusions; Improve the quality of mold and core sand, and improve the concession of sand mold and core; Extend the unpacking time of castings to make castings cool slowly in the mold; Aging treatment shall be carried out for castings to reduce residual stress.
For more information about enameled cast iron, smithey cast iron, crofton cast iron, plz feel free to contact us.